Nitrogen Oven adopts liquid crystal microcomputer intelligent PID temperature controller with multiple data display, menu operation interface, easy to use, precise temperature control and small fluctuation. With temperature correction, over-temperature alarm, timer setting, call recovery, parameter memory and other functions. Oxygen-free nitrogen-filled oven is mainly used for baking and aging test in high-temperature clean and oxygen-free environment of materials in electronics, chemical, materials, lithium, ceramics and other industries.
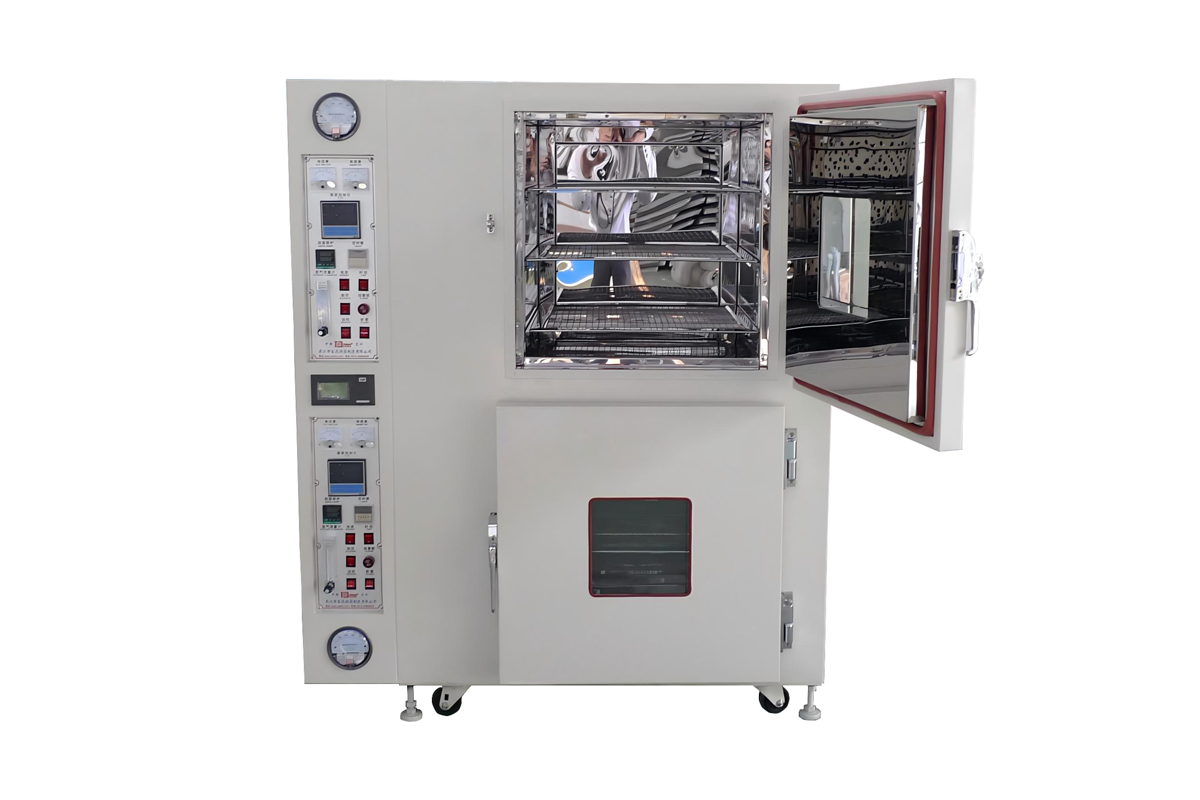
Equipment features
1. The box body is made of ceramic fiber heat preservation, which has the characteristics of fast warming and energy saving.
2. The inner liner adopts full welding treatment, the pipeline adopts seamless stainless steel pipe fittings welding treatment, the oxygen concentration can reach 100PPM.
3. Adopting fan forced ventilation, the oven is equipped with air ducts, temperature uniformity of 1.5℃%, uniform drying of materials, the air inlet adopts high temperature and high efficiency filters to ensure the cleanliness requirements.
4. Delta temperature control system, PID automatic algorithm, temperature control accuracy ± 0.5 ℃.
5. Dual flow meter nitrogen saving system, dual delay nitrogen filling control, oxygen-free, low oxygen environment greatly saves nitrogen consumption.
6. Oxygen-free oven, can achieve ≤ 50ppm oxygen content, due to its sealing and into the nitrogen distribution, air duct design, exhaust position design, are designed after digital modeling simulation.
7. Oxygen-free oven door is a double seal structure, at the same time can realize the function of rapid oxygen reduction, rapid temperature rise and fall.
8. Adjustable inert gas air transportation system, including flow meter, two-way gas control valve, cycle start high-flow air transportation and low-flow regulation.
9. Adjustable wind speed, to ensure the adaptation to different categories of products.
10. 100K encrypted aluminum silicate rock wool insulation to ensure the surface temperature of the box.
11. Independent over-temperature protection, as well as ground fault protection.
12. Horizontal circulation air transport system and electric heating system can realize the performance of temperature uniformity.
13. Optional accessories:
① Multi-point temperature measurement view and record function;
② Oxygen content analyzer;
③ Networking function;
④ HEPA high efficiency filter;
⑤ Rapid cooling system
Specification | Description |
---|
Temperature Range | Ambient to 300°C (572°F), higher temperatures available upon request |
Nitrogen Flow Rate | Adjustable, typically 0-20L/min depending on oven model |
Chamber Size | Available in various sizes, from small bench-top to large industrial chambers |
Temperature Control Accuracy | ±1°C (±2°F) for precise temperature control |
Heating System | Electric heating with uniform temperature distribution |
Gas Inlet Type | Standard nitrogen gas inlet with pressure regulation |
Safety Features | Gas leak detection, over-temperature protection, and emergency shutoff |
Control System | Advanced digital controller with temperature and nitrogen flow adjustments |
Insulation | High-quality thermal insulation for energy efficiency |
Voltage | 220V, 50/60Hz (custom voltage options available) |
Benefits of Using a Nitrogen Oven:
1.Prevents Oxidation: The nitrogen atmosphere prevents oxidation and degradation of sensitive materials, which is especially important in the electronics, metals, and pharmaceutical industries.
2.Improved Product Quality: By providing an inert environment, the oven helps maintain the integrity of materials, improving the quality of the final product.
3.Enhanced Precision: Nitrogen ovens offer highly precise temperature control, ensuring consistent results for processes like curing, aging, and heat treatment.
4.Increased Safety: The nitrogen atmosphere helps reduce the risk of combustion or fire, making it safer than traditional ovens for certain processes.
5.Cost-Effective: With modern energy-efficient designs, nitrogen ovens offer low operational costs while maintaining high performance.
Specifications to Consider:
1.Temperature Range: Typically from ambient to 300°C, but higher temperatures can be achieved with specialized models.
2.Nitrogen Flow Rate: The rate at which nitrogen gas is introduced into the oven, often adjustable to suit different applications.
3.Chamber Size: Available in various sizes, from small bench-top models to large industrial ovens, depending on production needs.
4.Control System: Advanced controllers with digital displays, allowing precise adjustments of both temperature and nitrogen flow.
5.Safety Features: Gas leak detectors, over-temperature protection, and alarms for added safety during operation.