In the powder metallurgy (PM) industry, particularly in Metal Injection Molding (MIM), achieving high-quality, defect-free parts requires precise control over the production process. One of the most critical steps in this process is debinding, where the binder material that holds the metal powder together is removed before the part undergoes sintering to achieve its final strength and density. Nitrogen debinding Ovens play a crucial role in this stage, ensuring that the debinding process is carried out efficiently and without damaging the part.
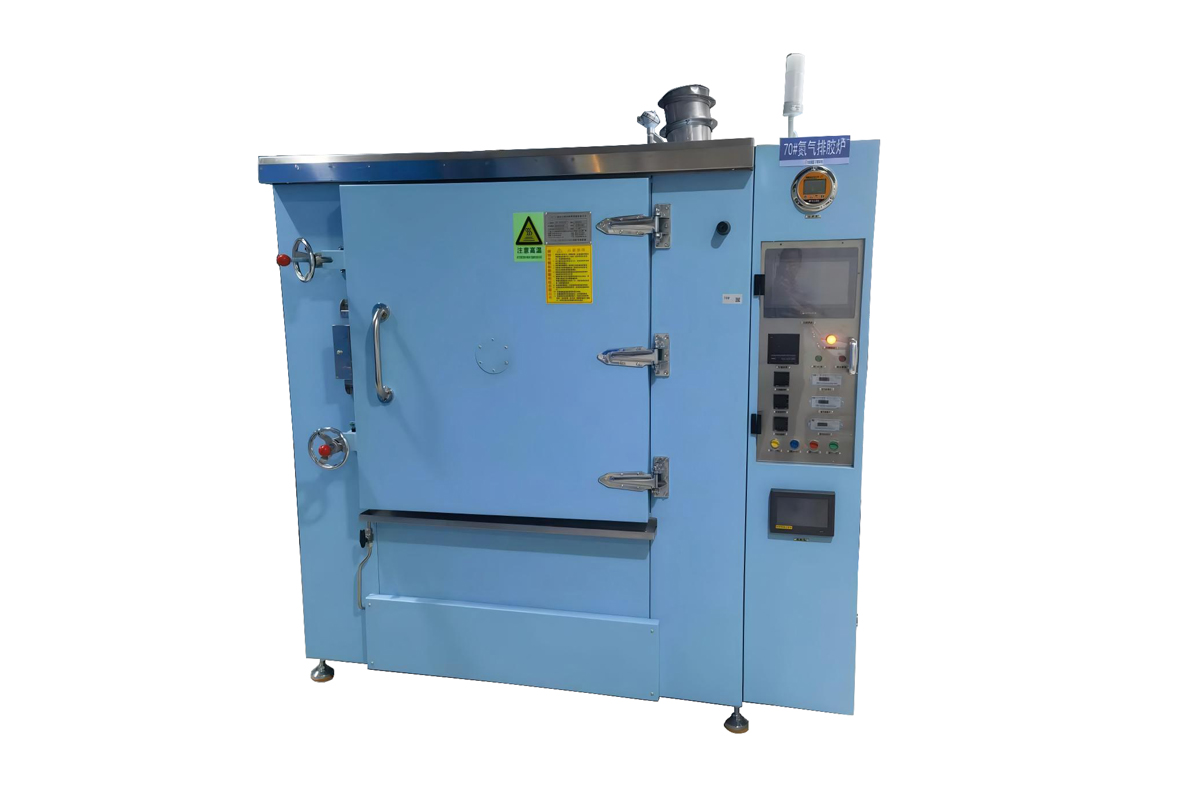
1. Understanding the Debinding Process in MIM
In MIM, metal powders are mixed with a binder (usually a combination of polymers) to create a feedstock that can be molded into intricate shapes. Once the parts are molded, the binder must be removed to allow the metal powders to fuse together during sintering. The debinding process is essential because if the binder is not removed properly, it can cause defects such as residual stresses, cracking, or incomplete sintering, leading to part failure.
2. The Role of Nitrogen in the Debinding Oven
Nitrogen debinding Ovens are specifically designed to perform this delicate binder removal process in an inert atmosphere, ensuring that oxidation or contamination does not occur. Nitrogen, being an inert gas, helps prevent oxidation of the metal powder during the heating and binder removal stages. In a typical nitrogen debinding Oven, the parts are placed in a chamber where they are subjected to controlled temperatures, while nitrogen gas is circulated to maintain a stable, non-reactive environment.
The controlled temperature and nitrogen atmosphere help to gradually decompose and vaporize the binder material without burning or damaging the parts. This gradual process ensures that the binder is removed evenly, avoiding issues such as part distortion or incomplete binder removal.
3. Benefits of Using Nitrogen Debinding Ovens in MIM
Prevention of Oxidation: As previously mentioned, nitrogen gas prevents oxidation of the metal powders during the debinding process. This is especially important for sensitive alloys or parts that require high-performance characteristics, as oxidation can degrade their mechanical properties and appearance.
Temperature Control: Nitrogen debinding ovens provide precise temperature control, which is essential for ensuring that the binder is removed at the correct rate. If the temperature is too high, the binder can decompose too quickly, causing parts to crack or warp. If it's too low, the binder may not be removed completely, which can lead to problems during sintering.
Efficient Binder Removal: The combination of temperature control and a nitrogen atmosphere ensures that the binder is removed in a consistent and efficient manner. This is crucial for MIM parts, which often have complex geometries and small features that are prone to distortion if not debound correctly.
Pre-sintering Preparation: By removing the binder effectively, nitrogen debinding ovens prepare the parts for the sintering stage, where the metal powder particles fuse together to create a solid, high-strength component. Proper debinding ensures that the sintering process goes smoothly, leading to parts with excellent density and mechanical properties.
4. Applications in Various MIM Materials
Nitrogen debinding ovens are used to process a wide range of materials in MIM, including various stainless steel, tungsten, titanium, nickel, and iron-based alloys. Each of these materials has unique debinding requirements, and nitrogen debinding ovens can be customized to accommodate the specific needs of different powders and binder systems.
For example, stainless steel parts may require a slightly different temperature profile compared to titanium or nickel parts due to their differing thermal properties. The nitrogen debinding oven's ability to maintain a controlled atmosphere and temperature ensures that each material is debound according to its requirements, minimizing the risk of defects.
5. Enhancing Productivity in MIM
Another key application of nitrogen debinding ovens in MIM is their contribution to increased productivity. These ovens are designed to handle high throughput, which is critical in mass production environments. They can process multiple parts simultaneously, and their automated controls ensure consistent results across large batches.
By removing binders efficiently and preparing parts for sintering in a timely manner, nitrogen debinding ovens help optimize the overall production cycle, reducing downtime and improving the overall efficiency of the MIM process.
6. The Future of Nitrogen Debinding Ovens in MIM
As the MIM industry continues to grow, the need for more advanced debinding technologies becomes increasingly important. Manufacturers are focusing on improving the efficiency, energy consumption, and automation of nitrogen debinding ovens. Innovations in oven design, temperature control systems, and gas circulation technologies are allowing for more precise and energy-efficient debinding processes.
Additionally, as new materials and binder systems are developed for MIM, nitrogen debinding ovens will continue to evolve to meet the changing needs of the industry. The development of advanced sensors and AI-driven control systems will further enhance the precision and consistency of debinding, pushing the boundaries of what can be achieved in MIM.
In the powder metallurgy industry, especially in Metal Injection Molding (MIM), nitrogen debinding ovens are an essential tool for achieving high-quality parts. By providing a controlled nitrogen atmosphere and precise temperature regulation, these ovens ensure the efficient and safe removal of binders from metal powders, preparing the parts for the sintering process. The benefits of using nitrogen debinding ovens, such as oxidation prevention, temperature control, and increased productivity, make them a critical component in the MIM process. As the industry advances, nitrogen debinding technology will continue to evolve, supporting the production of more complex, higher-performance components.