In the ever-evolving landscape of manufacturing, energy efficiency has become more than just a buzzword; it’s a critical factor that impacts operational costs and environmental sustainability. Among the key players in high-tech manufacturing, clean Tunnel Furnaces have emerged as essential tools, especially in industries where precision and cleanliness are paramount. But what truly sets these furnaces apart is their ability to maximize energy efficiency, ultimately leading to substantial savings and enhanced productivity.
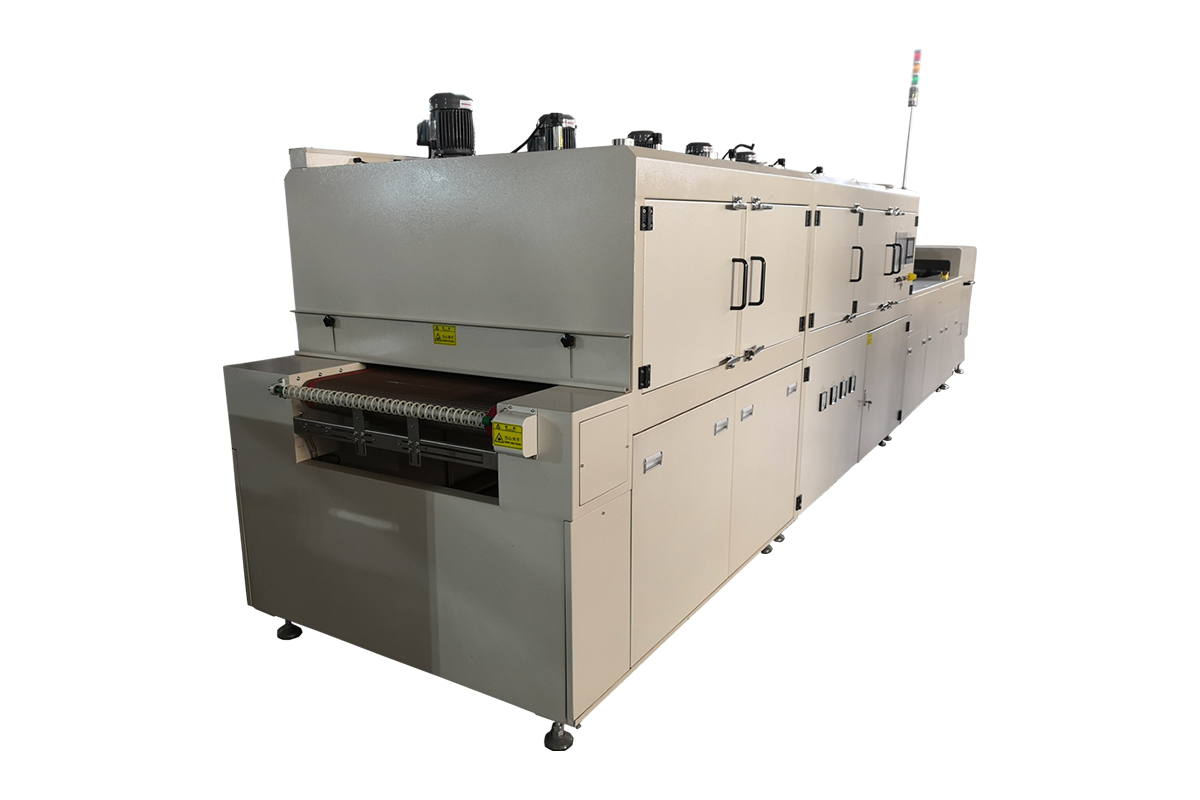
The Importance of Energy Efficiency
Before diving into the specific technologies that enhance energy efficiency in Clean Tunnel Furnaces, let’s consider why this aspect is so vital. With energy costs on the rise, manufacturers are increasingly seeking ways to reduce consumption without compromising quality. In sectors like semiconductor manufacturing, pharmaceuticals, and aerospace, where clean environments are necessary, the energy demands can be particularly high. Thus, implementing energy-efficient technologies not only lowers operational costs but also contributes to a company’s sustainability goals.
Key Energy-Saving Technologies
1. Advanced Insulation
One of the most significant contributors to energy efficiency in Clean Tunnel Furnaces is advanced insulation. High-quality insulation materials reduce heat loss, allowing furnaces to maintain consistent temperatures with less energy input. This feature is crucial, as fluctuations in temperature can lead to product defects, necessitating costly reprocessing.
Manufacturers have started using aerogel insulation, which offers superior thermal resistance compared to traditional materials. This innovation minimizes energy waste and ensures that the heating elements do not have to work overtime to maintain desired temperatures, ultimately extending their lifespan.
2. Heat Recovery Systems
Another remarkable feature of modern Clean Tunnel Furnaces is the integration of heat recovery systems. These systems capture waste heat generated during the heating process and repurpose it for other functions, such as preheating incoming materials or supplying energy for other processes within the facility.
By recycling this energy, manufacturers can significantly reduce their overall energy consumption. For example, a facility that processes semiconductor wafers might use recovered heat to warm up cleaning solutions, thus saving on heating costs while enhancing process efficiency.
3. Variable Frequency Drives (VFDs)
Clean tunnel furnaces equipped with Variable Frequency Drives (VFDs) on their fans and pumps represent a substantial leap in energy efficiency. VFDs adjust the speed of motors based on demand, meaning that the furnace can operate at lower speeds during less intensive processing times.
This technology not only cuts down on energy use but also reduces wear and tear on mechanical components. As a result, manufacturers can enjoy lower maintenance costs and longer equipment lifespans, which further contributes to overall savings.
4. Smart Control Systems
The advent of smart technology in clean tunnel furnaces has revolutionized energy management. Modern control systems are equipped with sensors and algorithms that monitor various parameters in real time, such as temperature, airflow, and humidity.
By analyzing this data, the system can optimize the operation of the furnace automatically. For example, if a batch requires less heat, the system can reduce energy input accordingly. This level of adaptability means that energy is only used when and where it’s needed, preventing waste and ensuring optimal performance.
5. Efficient Heating Elements
The choice of heating elements plays a significant role in the energy efficiency of clean tunnel furnaces. Manufacturers are now favoring advanced ceramic or infrared heating elements, which provide rapid heat-up times and precise temperature control.
Unlike traditional electric coils, these elements can reach desired temperatures quickly and maintain them with minimal fluctuations. The faster turnaround times lead to reduced energy consumption during heating cycles, ultimately enhancing the furnace’s overall efficiency.
The Path Forward
As industries continue to grapple with rising energy costs and environmental concerns, the importance of energy efficiency in clean tunnel furnaces cannot be overstated. By embracing innovative technologies such as advanced insulation, heat recovery systems, VFDs, smart control systems, and efficient heating elements, manufacturers can achieve substantial operational savings while enhancing product quality.
Moving forward, it’s crucial for businesses to stay informed about the latest advancements in clean tunnel furnace technology. By doing so, they can ensure that they are making informed decisions that benefit not only their bottom line but also the environment.
Energy efficiency in clean tunnel furnaces represents a transformative opportunity for manufacturers across various sectors. By adopting energy-saving technologies, businesses can significantly reduce operational costs, enhance product quality, and contribute to sustainability efforts. As the industry progresses, the focus on energy efficiency will likely become even more pronounced, making clean tunnel furnaces a cornerstone of modern manufacturing. The journey toward greater efficiency is not just beneficial—it’s essential for thriving in an increasingly competitive landscape.