Infrared (IR) heating technology has revolutionized various manufacturing processes by providing efficient and uniform heating solutions. Among the key factors influencing the performance of IR Infrared Furnaces, precise temperature control and monitoring systems play a critical role in ensuring product quality.
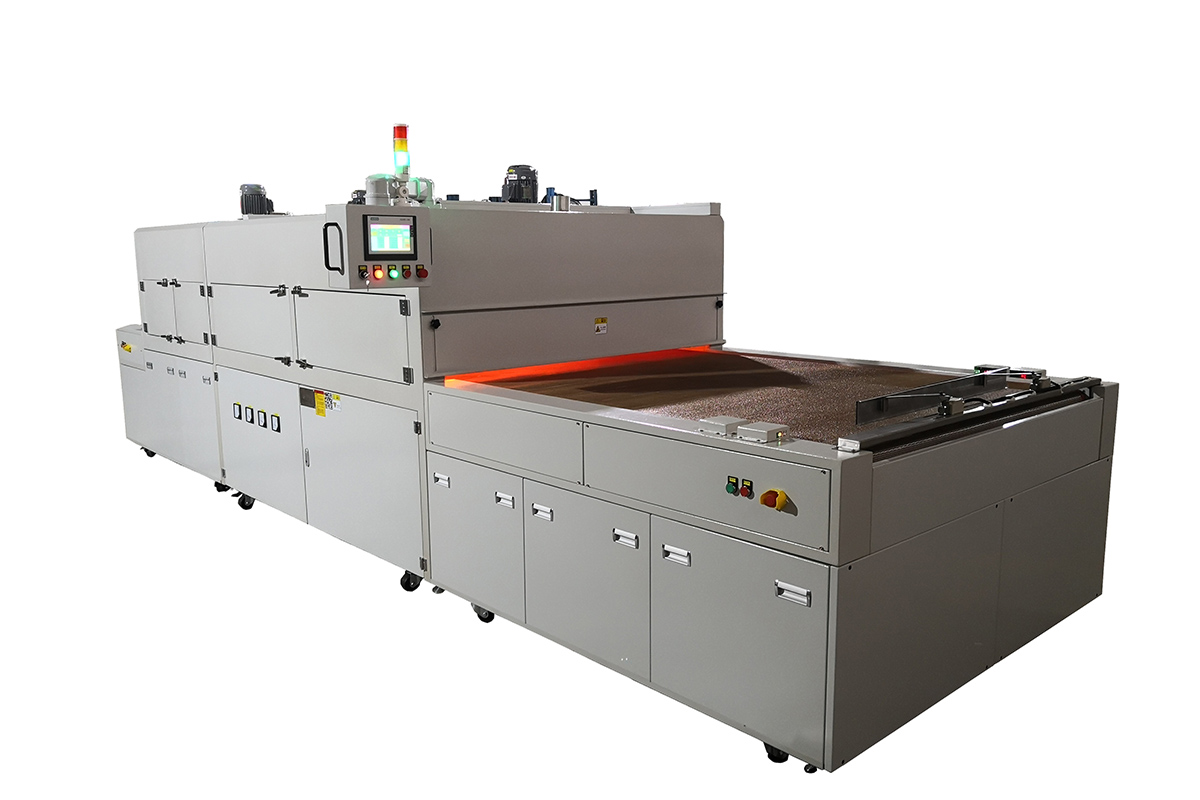
Importance of Precise Temperature Control
Uniform Heating: One of the primary advantages of IR Infrared Furnaces is their ability to heat materials uniformly. Precise temperature control ensures that all parts of the material receive consistent thermal energy, which is crucial in processes like curing, drying, and sintering. Uniform heating helps prevent defects such as warping, cracking, or uneven surface finishes, which can compromise product integrity.
Quality Assurance: In many industries, including semiconductor manufacturing, ceramics, and metal treatments, maintaining specific temperature profiles is essential for product quality. For instance, in semiconductor fabrication, exact temperatures are required during processes such as annealing to achieve desired electrical properties. Inaccurate temperature control can lead to subpar results, resulting in costly rework or scrapped materials.
Material Properties: Different materials respond differently to heat, and their mechanical and chemical properties can change significantly with temperature variations. Precise temperature control allows manufacturers to tailor heating processes to specific materials, ensuring that the desired properties—such as strength, flexibility, and conductivity—are achieved. This adaptability is particularly important in applications involving composite materials and advanced ceramics.
Process Optimization: Accurate temperature monitoring systems enable manufacturers to optimize their processes. By continuously tracking temperature variations, operators can adjust parameters in real time to achieve optimal heating rates and minimize cycle times. This not only enhances productivity but also improves energy efficiency, as manufacturers can avoid unnecessary energy consumption due to overheating or prolonged heating cycles.
Monitoring Systems and Technology
Modern IR Infrared Furnaces are equipped with sophisticated monitoring systems that provide real-time data on temperature levels. These systems often include:
Thermocouples and Infrared Sensors: These devices accurately measure surface temperatures of the material being heated. Thermocouples are commonly used for direct contact measurements, while infrared sensors can gauge temperatures without physical contact, making them ideal for delicate materials.
Programmable Logic Controllers (PLCs): PLCs integrate temperature data from sensors to automate heating processes. They can be programmed to maintain specific temperature profiles, ensuring that heating cycles are followed precisely.
Data Logging and Analytics: Many modern IR furnaces feature data logging capabilities that allow manufacturers to analyze temperature trends over time. This data can be invaluable for identifying patterns, troubleshooting issues, and implementing process improvements.
In conclusion, precise temperature control and monitoring systems are essential components of Ir Infrared Furnaces that significantly influence product quality and manufacturing efficiency. By ensuring uniform heating, maintaining critical material properties, and enabling process optimization, these systems contribute to the overall success of various industrial applications. As manufacturers continue to embrace IR heating technology, the importance of advanced temperature control solutions will only increase, further driving innovation and quality in the manufacturing landscape.