In industrial heating processes, temperature uniformity is a critical factor that directly impacts product quality, energy efficiency, and production stability. In advanced tunnel Ovens—especially multi-layer chain tunnel Ovens—forced hot air circulation plays a vital role in achieving this uniformity.
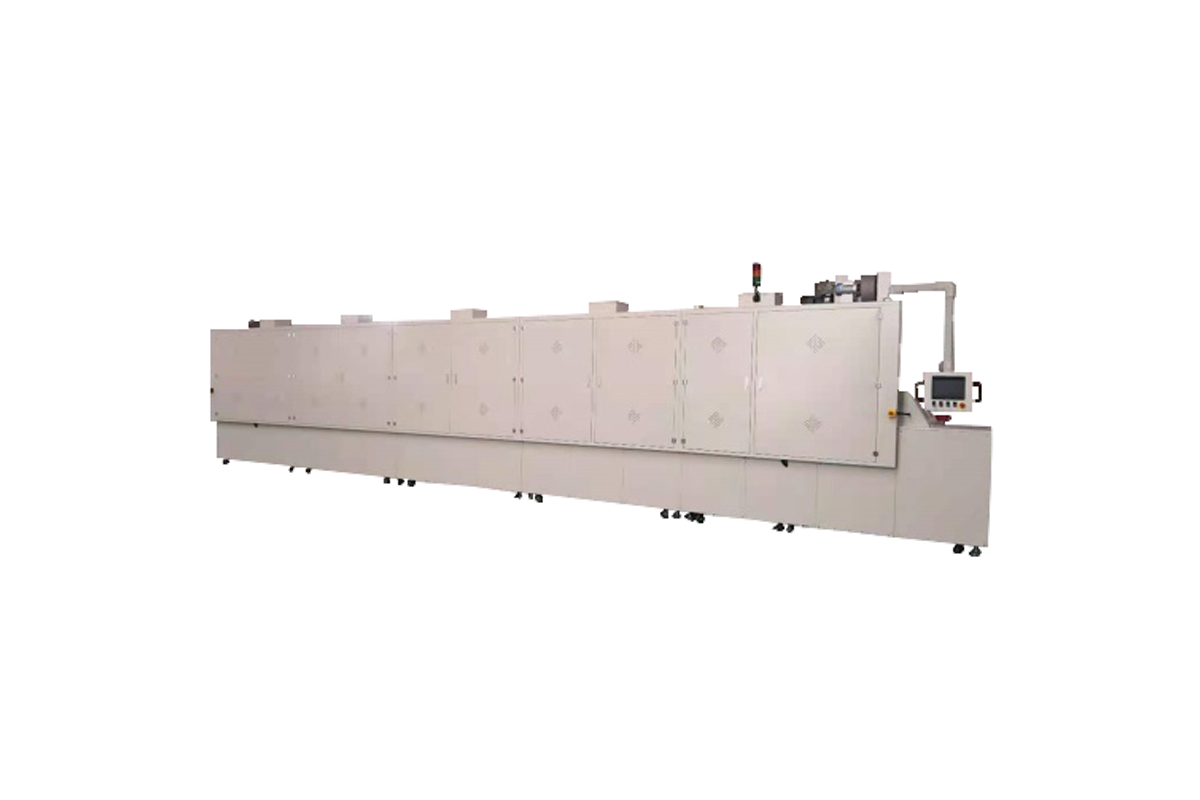
What Is Forced Hot Air Circulation?
Forced hot air circulation is a system that uses centrifugal fans or blowers to move heated air rapidly and evenly throughout the interior of the Oven. Unlike natural convection, where hot air rises slowly and may create uneven temperature zones, forced circulation ensures that the heat is distributed dynamically, reaching every corner and layer of the Oven chamber.
Why Temperature Uniformity Matters
Inconsistent heating leads to:
Uneven drying or curing of materials
Increased defect rates, especially in temperature-sensitive industries such as lithium battery, electronics, or food processing
Energy waste, as more heat is required to compensate for cooler zones
Extended production cycles, reducing overall throughput
Maintaining a uniform temperature within ±1.5% (as achieved in quality-designed multi-layer tunnel ovens) ensures reliable, repeatable outcomes across all product batches.
How Forced Hot Air Circulation Works in Tunnel Ovens
1.Air Distribution Design
The oven’s ductwork and air outlet layout are engineered to guide hot air flow across each layer of the conveyor. In multi-layer designs, separate circulation loops or directional vanes may be used for top and bottom layers.
2.Centrifugal Fans for Dynamic Flow
High-powered fans installed at strategic points create a high-volume, closed-loop air movement. This eliminates hot or cold spots by continuously mixing and redistributing the air.
3.Precision Heating Response
Paired with intelligent temperature control systems (such as PLC+HMI and PID algorithms), the forced air circulation helps quickly stabilize any temperature fluctuations, especially during load changes.
4.Optimized Heat Recovery
The circulating hot air can also pass through heat exchangers or be partially recirculated, reducing the need for continuous heating and improving energy efficiency.
Advantages in Multi-Layer Tunnel Oven Design
1.Layer-by-layer consistency: Each conveyor level receives an equal amount of heated air, critical when drying lithium battery electrodes, baking food, or curing coated surfaces.
2.Shorter heating cycles: Uniform heating allows for faster ramp-up and reduced residence time.
3.Improved product quality: From moisture-sensitive food to thermosensitive polymers, consistent thermal conditions ensure uniform appearance, strength, and integrity.
Industry Applications That Rely on Uniform Heat
1.Lithium Battery Production: Electrode foil drying requires precise thermal control to avoid cracking or delamination.
2.Food Processing: Uneven baking or dehydration can affect shelf life and taste.
3.Electronics: Solder paste preheating or component curing needs tight thermal tolerances.
4.Chemicals & Composites: Stable temperatures improve the structural formation of sensitive compounds.
In the realm of industrial thermal processing, forced hot air circulation is not just a performance feature—it’s a foundational element that ensures consistent results and operational reliability. For multi-layer chain tunnel ovens, this technology maximizes temperature uniformity, enabling manufacturers to scale up production without compromising product quality.