In industries such as semiconductor packaging, electronics assembly, and precision circuit board manufacturing, Glue Discharge Ovens play a vital role in removing residual adhesives from components or substrates through controlled high-temperature heating. Choosing the right Oven directly impacts product quality, process efficiency, and long-term reliability. Here are the key features you should look for when selecting a high-quality Glue Discharge Oven for your production line.
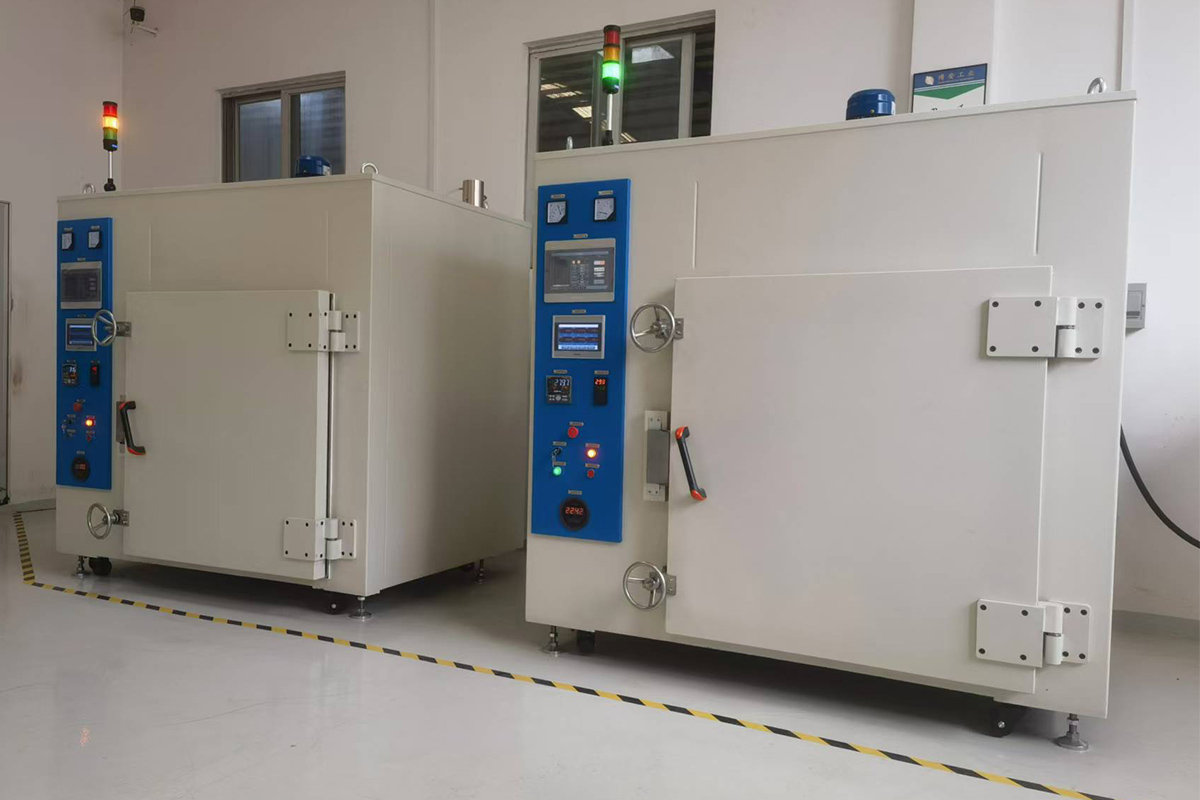
1. High-Temperature Stability and Uniformity
One of the most critical factors is the Oven's ability to maintain a consistent temperature throughout the entire chamber. Look for ovens equipped with:
PID temperature control systems with precision sensors
±1°C temperature deviation tolerance or better
Multi-point heating zones to reduce temperature gradients
Uniform thermal distribution ensures complete and even glue evaporation, especially important for delicate electronics or multilayer assemblies.
2. Intelligent Temperature Control System
Modern glue discharge ovens come with programmable control interfaces (PLC or touch screen HMI), enabling:
Customized multi-stage heating profiles
Automatic start/stop cycles for scheduled production
Real-time monitoring and error alerts
Data logging and export for quality traceability
This smart control system not only enhances precision but also improves operator usability and consistency in batch production.
3. Programmable Temperature Curve Setting
Advanced ovens allow engineers to set up ramp-soak temperature profiles, where temperature increases, holds, or cools down at pre-defined intervals. This feature is essential for:
Matching different glue discharge or resin curing needs
Preventing thermal shock in sensitive materials
Improving the adaptability for different production requirements
Some systems also support 99-step memory, allowing the storage and recall of common recipes.
4. Efficient Hot Air Circulation System
To promote even heating and efficient glue discharge, an oven should include a forced hot air convection system:
Axial or centrifugal fan designs for consistent airflow
Air circulation ducts that prevent dead zones
Quick heat recovery after door opening
Efficient airflow ensures rapid drying, prevents local overheating, and optimizes production cycle time.
5. Optimized Exhaust and Ventilation System
During glue discharge, volatile organic compounds (VOCs) or fumes are released. A high-performance oven will include:
Adjustable exhaust ports or ducts
Active extraction systems to remove fumes
Optional HEPA or activated carbon filters
This not only maintains operator safety but also ensures compliance with environmental regulations.
6. Anti-Static and Dust-Proof Structure
In microelectronics or IC packaging, electrostatic discharge (ESD) can damage sensitive components. A quality oven should offer:
Anti-static coatings or grounded chambers
Sealed doors with silicone gaskets
Stainless steel inner chambers to reduce particle accumulation
These structural features help maintain a clean and ESD-safe processing environment.
7. Durable Build Quality and Safety Protection
Choose ovens with robust components such as:
High-temperature resistant 304/316 stainless steel interiors
Overheat protection, emergency shutdown, and auto-lock doors
CE, UL, or ISO certifications for compliance and reliability
Durability ensures longevity, while comprehensive protection systems reduce the risk of accidents or downtime.
Investing in a high-quality Glue Discharge Oven isn't just about reaching high temperatures—it's about precise control, safe operation, consistent performance, and long-term efficiency. Whether you're manufacturing semiconductors, LED modules, or multilayer PCB boards, selecting the right oven with the right features can significantly improve your throughput, product quality, and ROI.