In the world of UV curing technology, precision and adaptability are crucial for ensuring optimal results. One of the key benefits of Non-Standard Customization UV Machines is their ability to provide adjustable UV intensity and curing time. This flexibility enables manufacturers to fine-tune the curing process for different materials, thicknesses, and application requirements, optimizing the efficiency and quality of the curing process. In this article, we will explore the significance of these adjustable features and how they contribute to improved performance in UV curing applications.
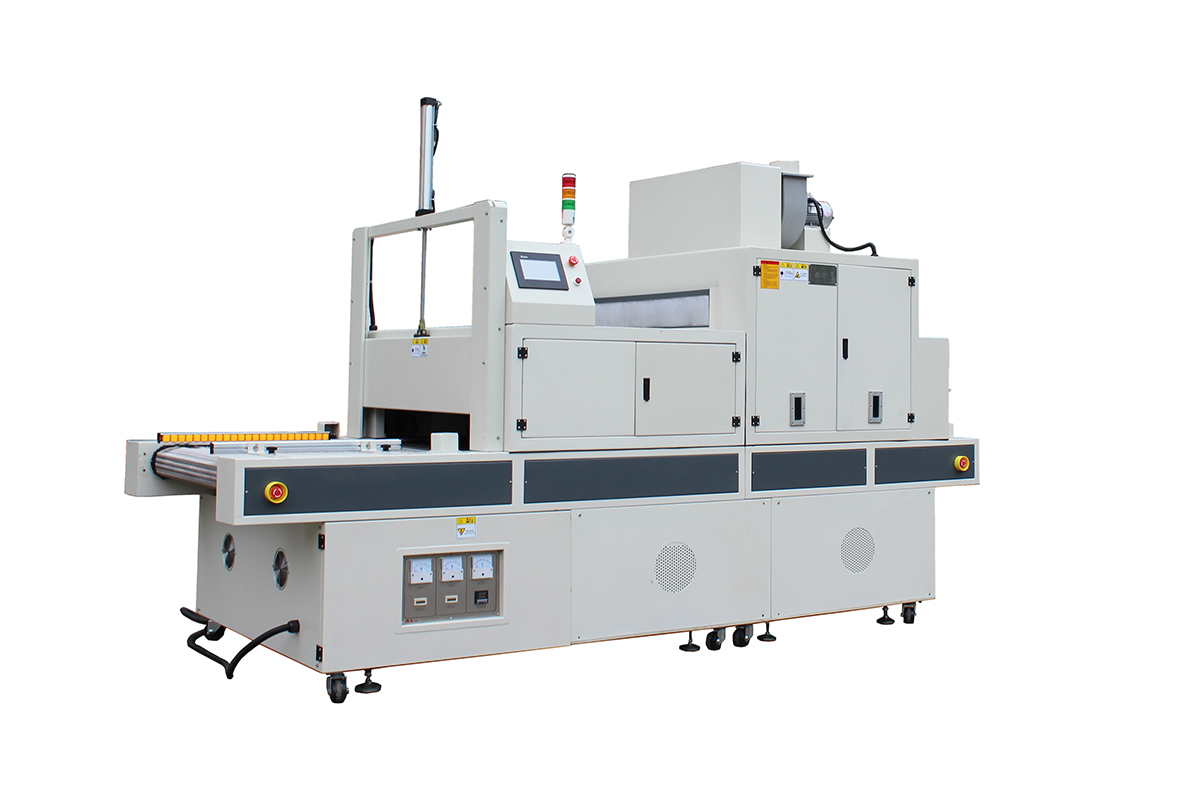
1. Understanding UV Curing
UV curing is a process that uses ultraviolet (UV) light to initiate a chemical reaction, causing certain materials (such as inks, coatings, adhesives, and resins) to harden or cure quickly. Unlike conventional drying methods, UV curing offers faster processing times and more durable results. The technology is used in various industries, including printing, electronics, automotive, and packaging.
However, UV curing is not a one-size-fits-all solution. Different materials react to UV light in varying ways, and curing conditions must be carefully controlled to achieve the desired outcome. This is where adjustable UV intensity and curing time come into play.
2. The Role of Adjustable UV Intensity
UV intensity refers to the amount of UV light energy emitted by the UV Machine. It directly influences the curing speed and the depth of penetration into the material being cured. The adjustability of UV intensity in non-standard customization UV Machines allows manufacturers to tailor the curing process to the specific needs of different applications.
Why Adjustable UV Intensity Matters:
Material-Specific Requirements: Different materials, such as plastics, metals, or paper, require varying levels of UV exposure to achieve effective curing. For example, a delicate material might require lower UV intensity to avoid surface damage, while a thicker material may need higher intensity to cure thoroughly.
Thickness of the Coating: The thickness of the layer being cured can impact the necessary UV intensity. Thicker coatings require more UV light to penetrate and cure the entire surface. Adjustable intensity ensures that both thin and thick layers can be effectively cured without overexposure or underexposure.
Enhanced Curing Speed and Efficiency: By adjusting UV intensity, operators can optimize curing speed, improving overall production efficiency. For high-throughput environments, faster curing without sacrificing quality is a significant advantage.
Key Benefits of Adjustable UV Intensity:
Customized Curing for Different Materials: The ability to adjust UV intensity allows for precise control over how each material reacts to UV light, ensuring the desired curing effect.
Reduced Risk of Material Damage: Adjusting UV intensity helps prevent overexposure, which can lead to material degradation, discoloration, or warping.
Energy Efficiency: By tailoring the UV intensity to the specific curing needs, manufacturers can reduce energy consumption, making the process more cost-effective and environmentally friendly.
3. The Importance of Adjustable Curing Time
Curing time is the amount of time the material is exposed to UV light during the curing process. The adjustable curing time in non-standard UV machines gives operators the ability to control how long the material is exposed to UV radiation. This flexibility is essential because the curing process is not instantaneous; it requires sufficient exposure to ensure that the material is fully hardened.
Why Adjustable Curing Time is Crucial:
Varying Material Reactions: Different materials may require more or less time to cure depending on their chemical composition. For example, some materials may harden quickly, while others may take longer to fully cure. Adjustable curing time ensures that each material receives the appropriate amount of exposure.
Preventing Incomplete Curing: Insufficient exposure time may result in incomplete curing, leading to soft spots, tackiness, or even adhesion failures. Conversely, excessive curing time can lead to surface degradation or unnecessary energy consumption. Adjusting the curing time allows manufacturers to find the perfect balance.
Customization for Complex Applications: For intricate or multi-layered applications, adjustable curing time helps to ensure that all areas, including deeper layers, receive adequate exposure to UV light, achieving uniform curing throughout.
Key Benefits of Adjustable Curing Time:
Optimized Curing for Complex Applications: By fine-tuning curing time, manufacturers can ensure that all layers and areas of a product are evenly cured, resulting in consistent quality across the entire production run.
Preventing Over-Curing: Excessive curing time can cause materials to become brittle or discolored. Adjustable curing time allows for precise control, preventing over-curing and ensuring the material maintains its integrity.
Increased Process Flexibility: The ability to adjust curing time provides manufacturers with the flexibility to handle a wide variety of materials, products, and production processes, from fast curing of simple layers to longer curing times for intricate coatings.
4. Applications of Adjustable UV Intensity and Curing Time
The ability to adjust both UV intensity and curing time offers a significant advantage in various industries and applications:
Printing Industry: In the printing industry, different types of inks and coatings have specific curing requirements. Adjustable UV intensity and curing time help achieve the desired finish without compromising the quality or durability of printed materials.
Electronics Manufacturing: In the electronics industry, UV curing is used for encapsulating components, securing adhesives, and coating printed circuit boards (PCBs). The ability to adjust curing parameters ensures that sensitive electronic components are not damaged during the curing process.
Automotive and Industrial Coatings: For automotive parts or industrial components, where thicker coatings are often applied, adjustable UV intensity and curing time ensure that the coating is cured uniformly and to the required specifications.
Packaging Industry: In the packaging sector, particularly for flexible packaging or labels, precise control over curing ensures that materials like plastic and paper are cured effectively without damaging the substrate.
5. Conclusion: Enhancing Performance with Adjustable Features
Non-Standard Customization UV Machines equipped with adjustable UV intensity and curing time offer significant benefits in terms of precision, flexibility, and overall process optimization. These features allow manufacturers to:
Tailor the curing process to the unique needs of different materials and applications.
Achieve consistent, high-quality results with minimal risk of material damage or incomplete curing.
Improve energy efficiency and reduce operational costs by optimizing curing parameters for each specific job.
Incorporating these adjustable features into UV curing processes not only enhances the performance and versatility of the equipment but also allows manufacturers to stay competitive in an increasingly demanding and diverse industrial landscape. Whether in printing, electronics, automotive, or packaging, adjustable UV intensity and curing time are essential tools for achieving the best possible results and ensuring the highest standards of quality in the final product.