In the world of electronics manufacturing, the durability, performance, and longevity of components are of utmost importance. Whether it’s circuit boards, connectors, or intricate electronic devices, ensuring their protection against environmental factors such as moisture, dust, and corrosion is vital. This is where coating Ovens come into play. These specialized Ovens are essential for curing protective coatings on electronic components, providing a crucial layer of defense that enhances their reliability and functionality.
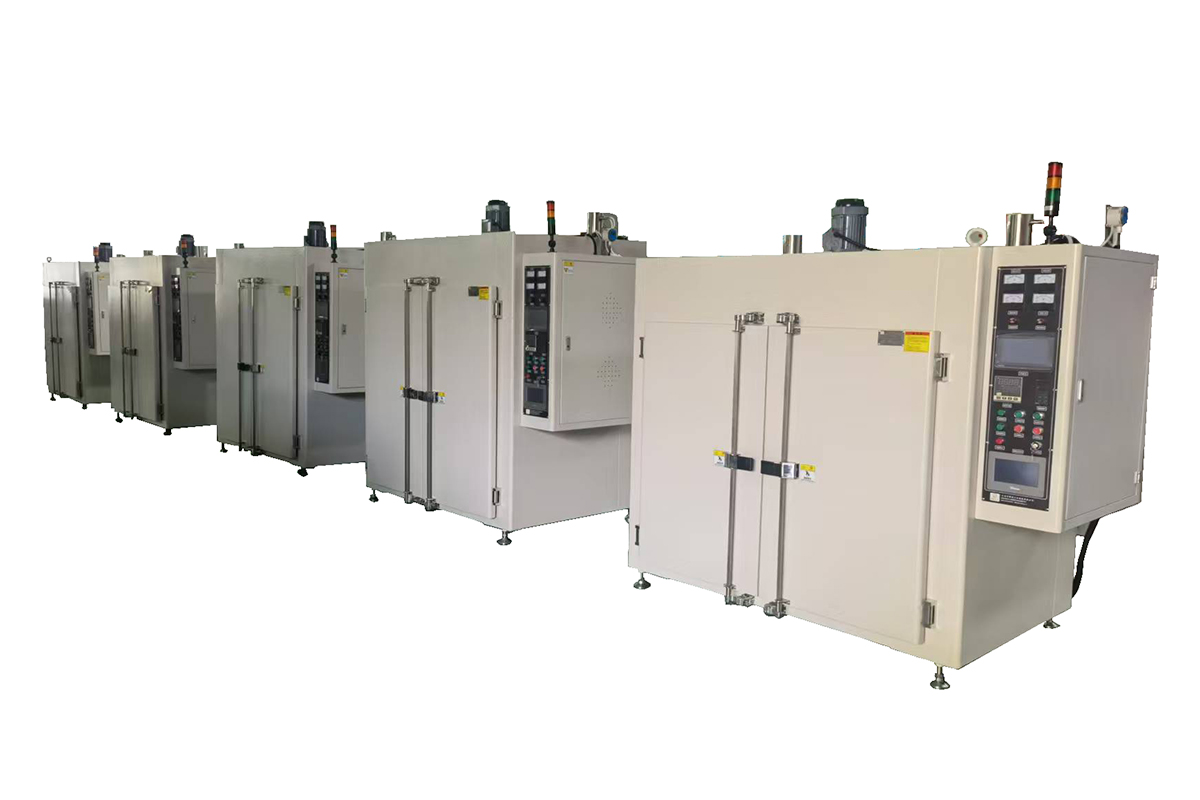
The Role of Coating Ovens in Electronics Manufacturing
Coating Ovens are used to cure protective coatings, such as conformal coatings, which are applied to electronic circuit boards, components, and devices. These coatings serve multiple functions, such as:
1.Moisture Protection:Electronics are vulnerable to moisture, which can cause short circuits, corrosion, and component degradation. Coatings applied to the surface of these components create a moisture-resistant barrier, ensuring that they continue to function reliably even in humid or damp environments.
2.Dust and Contaminant Resistance:During production or in their end-use environments, electronic components may be exposed to dust or other particulate contaminants. Conformal coatings act as a shield, preventing dust accumulation that could interfere with the performance of sensitive circuits.
3.Corrosion Prevention:Metals, especially in electronic connectors, are prone to oxidation and rust, particularly when exposed to moisture or corrosive chemicals. Protective coatings help prevent this corrosion, extending the lifespan of electronic devices.
4.Thermal Management:Many electronic components generate heat during operation. Some coatings also provide a degree of thermal management, helping to dissipate heat away from sensitive areas, thereby preventing overheating.
5.Electrical Insulation:Coatings can provide electrical insulation, preventing accidental short circuits or electrical interference between closely spaced components on circuit boards.
How Coating Ovens Enhance Coating Quality
Coating is only as effective as the curing process. A properly cured coating ensures maximum protection and durability, which is why coating ovens are critical in electronics manufacturing. Here’s how they improve the process:
1.Precise Temperature Control:Coating ovens are equipped with advanced temperature control systems, often using digital controllers or PLC-based systems. This ensures that coatings are cured at the optimal temperature, which varies depending on the type of material used. Precise temperature regulation is essential for ensuring that the coating adheres well and cures uniformly without cracking or peeling.
2.Uniform Heat Distribution:For coatings to cure evenly, uniform heat distribution within the oven is necessary. Coating ovens are designed with forced air circulation systems that ensure that the heat is evenly distributed throughout the chamber. This eliminates hot spots or cold spots, ensuring that every part of the coated component receives the same level of heat for consistent curing.
3.Energy Efficiency:Coating ovens are built with high-efficiency insulation to retain heat and minimize energy consumption. This is particularly important in electronics manufacturing, where the energy cost of curing processes can add up over time. Energy-efficient ovens help lower operating costs and reduce the environmental impact of manufacturing.
4.Customization:Electronics manufacturing often involves components of various sizes and shapes. Coating ovens are customizable, with options for rack configurations or conveyorized systems that allow different types of components to be processed efficiently. Customizable sizes and features make it easier for manufacturers to optimize production lines for various products.
5.Quick Turnaround Time:In today’s fast-paced manufacturing environments, minimizing production time is critical. Coating ovens provide quick curing cycles, ensuring that manufacturers can meet production deadlines without compromising quality. Faster turnaround times lead to increased productivity and more efficient manufacturing workflows.
Common Types of Coatings in Electronics
There are several types of coatings commonly used in electronics, each designed to meet specific protective needs:
1.Conformal Coatings:These coatings are applied to electronic circuit boards to provide protection against environmental stressors. They can be made from various materials, including acrylics, silicones, and polyurethanes.
2.Epoxy Coatings:Known for their strong adhesion and resistance to chemical damage, epoxy coatings are often used in harsh environments where corrosion or chemical exposure is a concern.
3.Polyurethane Coatings:Polyurethane coatings offer excellent flexibility and moisture resistance, making them ideal for applications that require protection from humidity and extreme temperatures.
4.Silicone Coatings:These coatings are often used in high-temperature applications due to their ability to withstand heat. They also offer flexibility and are ideal for components that experience thermal cycling.
Benefits of Using Coating Ovens in Electronics Manufacturing
1.Improved Reliability:By curing coatings evenly and thoroughly, coating ovens help ensure that electronic components remain reliable and functional throughout their lifespan. This is particularly important in critical applications such as medical devices, aerospace, and automotive electronics, where component failure can have serious consequences.
2.Enhanced Durability:The protection provided by coatings cured in coating ovens increases the lifespan of electronic products. This durability ensures that devices can withstand challenging environmental conditions, including moisture, heat, and vibration.
3.Cost-Effective Manufacturing:Using coating ovens to efficiently cure coatings can reduce manufacturing costs in the long run. The energy-efficient operation, reduced need for rework, and increased product reliability contribute to cost savings and improved profit margins.
4.Compliance with Industry Standards:Many industries, including automotive and aerospace, have strict standards for the quality and durability of electronic components. Coating ovens help ensure that products meet these standards, facilitating compliance with regulatory requirements.
5.Consistency and Quality Control:Coating ovens provide a controlled environment for curing coatings, ensuring that each component undergoes the same process and adheres to the same quality standards. This consistency is essential for manufacturers who need to maintain product quality across large batches.
Coating ovens play a pivotal role in electronics manufacturing by providing essential protection against environmental stressors and enhancing the overall performance and reliability of electronic components. With their ability to cure coatings uniformly, efficiently, and consistently, coating ovens ensure that electronics meet the rigorous standards required in today’s competitive market. Whether it’s providing moisture resistance, preventing corrosion, or improving thermal management, coating ovens are indispensable for maintaining the durability and functionality of modern electronic devices.