In today’s industrial landscape, energy efficiency has become a critical concern for manufacturers aiming to reduce operational costs and minimize their environmental footprint. The glue discharge Oven, an essential piece of equipment in industries such as automotive, electronics, packaging, and furniture manufacturing, plays a vital role in curing and drying adhesives. However, the energy consumption of these Ovens can be significant, which is why modern Glue Discharge Ovens are designed with a strong focus on energy efficiency.
This article explores the key features that contribute to the energy efficiency of modern glue discharge ovens, including heat recovery systems, optimal airflow designs, and advanced control technologies. It also delves into the environmental and cost-saving benefits of using energy-efficient ovens in manufacturing processes.
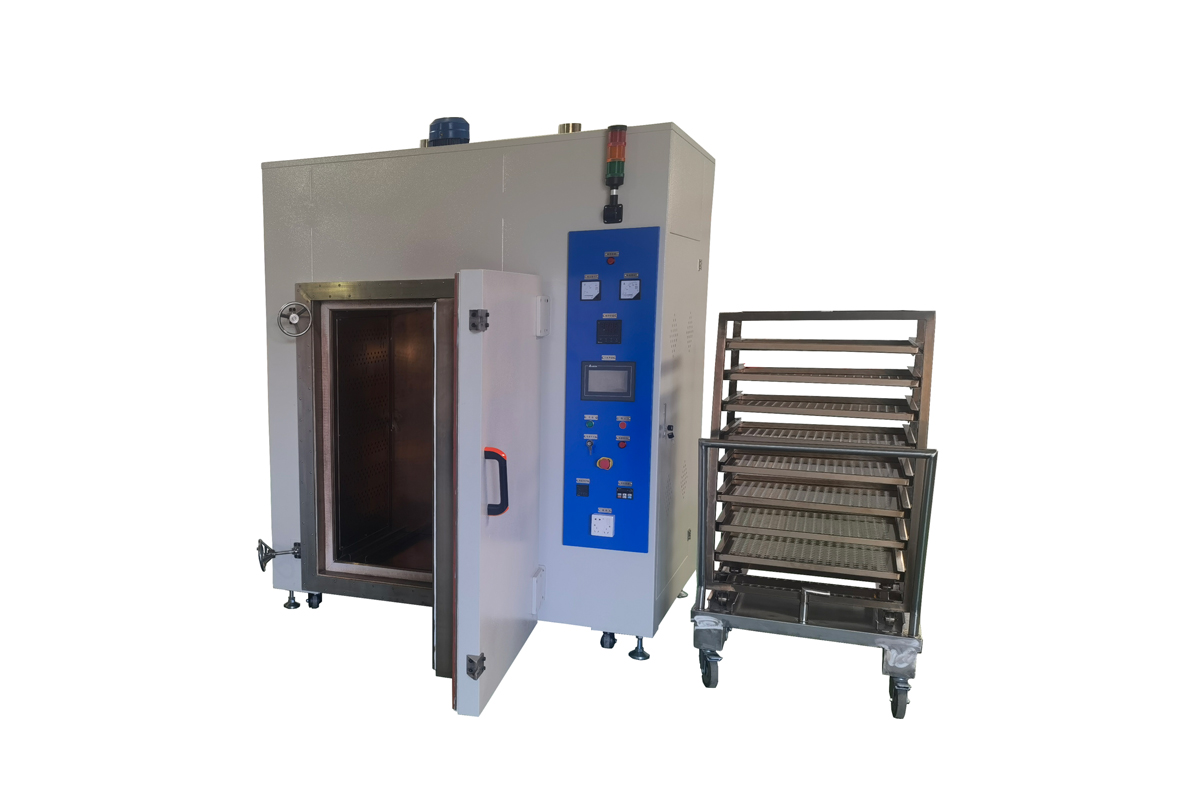
1. Heat Recovery Systems: Maximizing Energy Use
One of the most significant advancements in glue discharge ovens is the integration of heat recovery systems. These systems capture waste heat that would otherwise be lost during the curing or drying process and reuse it to maintain the desired temperature within the oven. Instead of relying entirely on external heating sources, the oven recycles its own heat, thus reducing the need for additional energy input.
Heat recovery systems typically work by transferring heat from exhaust air or other heat-generating components to pre-heat incoming air or materials. This not only reduces the energy needed for heating but also ensures that the oven reaches its target temperature more quickly, thereby improving the overall efficiency of the curing process.
Benefits:
Reduced energy consumption by using recovered heat.
Faster start-up times and consistent curing temperatures.
Lower operational costs due to decreased reliance on external energy sources.
2. Optimal Airflow Designs: Enhancing Temperature Distribution
Efficient airflow management is another essential aspect of energy-efficient glue discharge ovens. In traditional ovens, air circulation is often uneven, leading to hot spots, temperature imbalances, and longer curing times. Modern ovens, however, are equipped with forced air circulation systems that evenly distribute heat throughout the oven chamber.
These systems use strategically placed fans to ensure that air is circulated uniformly, promoting even adhesive curing. The improved airflow not only ensures consistent temperature across the entire surface of the material being processed but also reduces the need for extended curing times. By shortening the time required for adhesive drying, manufacturers can reduce energy consumption significantly.
Benefits:
Uniform curing of adhesives, ensuring product quality.
Faster curing times, which reduce energy usage and increase productivity.
Reduced energy wastage, as the oven operates more efficiently by minimizing temperature variations.
3. Advanced Control Technologies: Precision and Automation
Modern glue discharge ovens come equipped with advanced control technologies that allow for precise monitoring and adjustment of various parameters such as temperature, airflow, and curing time. These Intelligent Control Systems enable manufacturers to optimize energy consumption by adjusting settings based on the type of adhesive, the material being processed, and production requirements.
For example, ovens with PLC (Programmable Logic Controller) or touchscreen interfaces can be programmed to automatically adjust the temperature and airflow based on real-time data, ensuring that energy is only used when necessary. Additionally, many ovens feature automatic shut-off or energy-saving modes, where the oven reduces power consumption after the curing process is complete or when idle.
Benefits:
Precision control reduces energy waste.
Automated adjustments based on real-time requirements ensure energy is used efficiently.
Reduced downtime and energy consumption during non-operational periods.
4. Reduced Operational Costs: Long-Term Savings
The primary motivation for energy-efficient design in glue discharge ovens is the significant cost savings it brings. While energy-efficient ovens may have a slightly higher upfront cost, the long-term savings in electricity bills can offset this initial investment within a relatively short period. Manufacturers that implement energy-efficient technologies are also better positioned to meet energy usage regulations and reduce their environmental impact.
In addition to the direct savings on energy bills, an energy-efficient oven typically requires less maintenance, as optimized systems (such as heat recovery and circulation fans) reduce wear and tear. This results in lower maintenance costs and extends the lifespan of the equipment.
Benefits:
Lower energy costs due to reduced consumption.
Reduced maintenance expenses and longer equipment lifespan.
Return on investment (ROI) through energy savings over time.
5. Environmental Benefits: Reducing the Carbon Footprint
The global push towards sustainability and reduced carbon emissions has made energy-efficient technologies a priority for manufacturers across all industries. By adopting energy-efficient glue discharge ovens, manufacturers can significantly reduce their carbon footprint. These ovens require less electricity, which in turn lowers greenhouse gas emissions associated with electricity generation.
Moreover, the reduced heat output from efficient ovens means that less cooling is required, leading to even lower energy consumption in the overall manufacturing process. As industries strive to meet environmental standards and eco-conscious consumer demands, adopting energy-efficient equipment has become not just an economic advantage but a social responsibility.
Benefits:
Lower environmental impact by reducing energy usage and emissions.
Compliance with regulations on energy efficiency and sustainability.
Enhanced brand reputation as a company committed to eco-friendly practices.
6. Case Studies: Real-World Applications
To further illustrate the benefits of energy-efficient glue discharge ovens, let’s explore a few real-world examples of how these ovens are making a difference in various industries.
Electronics Manufacturing
In the electronics industry, where precise adhesive bonding is critical for circuit boards and components, energy-efficient glue discharge ovens have significantly reduced energy usage while maintaining the quality of bonding. Manufacturers report up to 30% energy savings compared to conventional ovens, translating into significant cost reductions.
Automotive Industry
Automotive manufacturers that use glue discharge ovens for bonding components such as windshields, trims, and interior parts benefit from optimized heat recovery systems. These ovens not only save energy but also speed up the curing process, which helps meet tight production schedules while cutting down on energy consumption.
Energy efficiency is no longer a luxury but a necessity for industries seeking to reduce operational costs, increase productivity, and contribute to a sustainable future. Modern Glue Discharge Ovens are designed with cutting-edge features like heat recovery systems, optimal airflow designs, and advanced control technologies, all aimed at minimizing energy consumption and improving overall performance.
By investing in energy-efficient ovens, manufacturers can enjoy significant cost savings, contribute to environmental sustainability, and improve their bottom line in the long term. As energy costs rise and environmental regulations become more stringent, adopting energy-efficient solutions is not just a smart choice – it's a competitive advantage.