This equipment is mainly used in electronics, semiconductor, touch screen, LCD, LED, PCB, hardware, plastic, aerospace materials, food, medicine, medical and other industries, IR Infrared Furnace is the use of infrared heaters as a heat source, through the direct radiation of infrared radiation to the product, so that the product can be quickly warmed up and heated, which is characterized by rapid heating, heating and uniformity, fast drying and curing products.
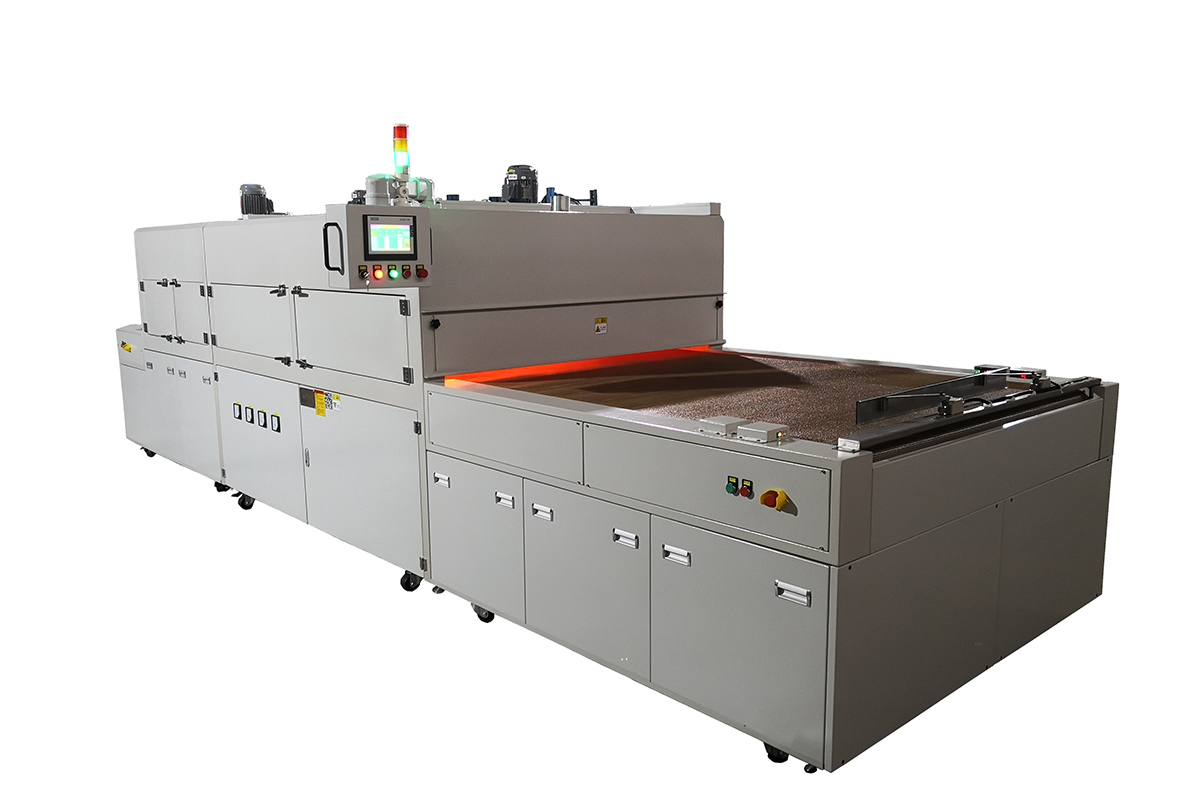
Equipment Features
1. Heating system: far-infrared heating, high radiation effect, faster heating speed, heating tube distribution is reasonable, each temperature zone independent control, according to the process needs of the heating section temperature
2. Temperature control system: PLC + solving touch screen control, using pulse output control heater, SSR, to avoid instantaneous current impact, temperature control fluctuations and other impacts, with DC24V output thermostat, which can make the output voltage smooth output, temperature control effect is more stable, the temperature is more accurate, with PID self-tuning, automatic thermostat, automatic timing can be more than the set value of the temperature, the automatic cutting off of the heating When the temperature exceeds the set value, it will automatically cut off the heating power and sound and light alarm.
3. Equipment insulation: 100K encrypted aluminum silicate rock wool insulation, the box outside the basic to maintain the normal temperature of the room, the ambient temperature has less impact.
4. Safety protection: leakage protection, line protection, short circuit protection, overload protection, over-temperature protection.
5. According to the production needs can be equipped with high-temperature resistant high efficiency filter, clean grade CLASS1000.
6. Conveying: Teflon mesh belt, stainless steel mesh belt or plate chain conveying can be selected according to the need, and the conveying speed can be adjusted by frequency conversion.
7. The interior of the furnace body is made of SUS304# stainless steel plate to keep clean inside the furnace, and the surface of the equipment is treated with baking paint.
8. Support product code tracing and MES system (optional).
Key Features
Infrared Heating Technology:
Uniform Temperature Distribution:
Energy Efficiency:
Quick Heating and Cooling Rates:
Temperature Control and Monitoring:
Advanced temperature control systems, including infrared sensors and programmable logic controllers (PLCs), enable precise monitoring and adjustment of the heating process. This ensures optimal processing conditions and reproducibility.
Versatile Applications:
IR Infrared Furnaces can accommodate a variety of materials, including metals, ceramics, polymers, and composites. This versatility makes them suitable for diverse applications across different industries.
Compact Design:
Low Emission Levels:
Applications
Semiconductor Manufacturing:
In the semiconductor industry, IR Infrared Furnaces are used for processes such as annealing, diffusion, and oxidation of silicon wafers. The precise heating capabilities ensure high-quality thermal processing.
Ceramics and Glass:
Metal Heat Treatment:
IR heating is used for processes like hardening, tempering, and brazing metals, improving their mechanical properties.
Composite Material Processing:
Food Industry:
In the food sector, infrared heating is applied for drying, cooking, and toasting processes, enhancing flavor and texture while reducing cooking times.
Material Testing:
Benefits
Enhanced Product Quality: The uniform heating and precise temperature control contribute to the consistent quality of processed materials.
Increased Production Efficiency: Quick heating and cooling rates improve cycle times, leading to higher throughput in manufacturing processes.
Lower Operating Costs: Energy efficiency translates to reduced operational costs, making IR Infrared Furnaces a cost-effective solution for thermal processing.
Adaptability: The versatility of IR furnaces allows them to be used across a wide range of materials and applications, accommodating the diverse needs of various industries.
FAQ
What is an IR Infrared Furnace?
It’s a heating device that uses infrared radiation to heat materials efficiently and uniformly.
How does infrared heating work?
It emits infrared radiation that directly heats objects without warming the surrounding air.
What are the advantages of using an IR Infrared Furnace?
Benefits include energy efficiency, uniform heating, quick temperature changes, and lower emissions.
Which industries use IR Infrared Furnaces?
Common in semiconductor manufacturing, ceramics, metal treatment, food processing, and material testing.
What materials can be processed?
Metals, ceramics, polymers, and composites.
How does it improve energy efficiency?
By directly heating materials, reducing heat loss and energy use.
Why is temperature control important?
It ensures uniform processing and consistent product quality.
What are the benefits of its compact design?
Saves space and allows for flexible integration into production lines.
Can IR Infrared Furnaces be automated?
Yes, many can be automated with sensors and controllers for improved efficiency.
What are future trends for IR Infrared Furnaces?
Trends include automation, improved energy efficiency, and wider material compatibility.