Industrial Ovens are essential tools in modern manufacturing and processing industries. Their ability to deliver precise temperature control, uniform heat distribution, and consistent performance makes them indispensable in sectors like automotive, aerospace, electronics, pharmaceuticals, and food processing. As industries evolve, the demand for reliable and efficient thermal processing solutions grows. A trusted Industrial Oven supplier plays a key role in meeting these needs by offering advanced technology, customizable solutions, and dependable service.
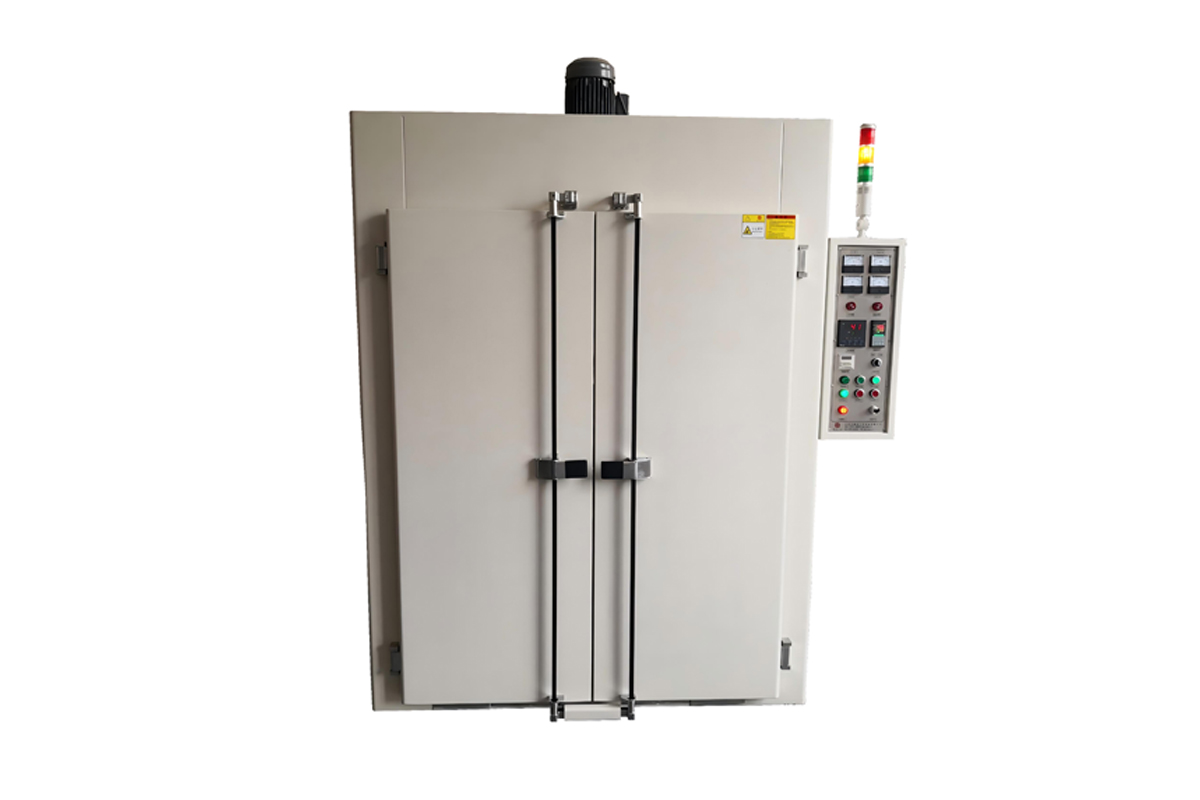
1.Wide Temperature Range: Industrial Ovens are capable of reaching temperatures from 100°C up to 1600°C, making them suitable for a wide variety of applications such as curing, drying, and heat treatment of materials.
2.Precision Temperature Control: With advanced control systems, industrial ovens ensure accurate temperature regulation, typically with an accuracy of ±1°C, which is essential for maintaining high-quality standards during production.
3.Even Heat Distribution: Equipped with air circulation systems, industrial ovens provide uniform heat distribution across the entire chamber, ensuring that materials are processed consistently.
4.Energy Efficiency: The use of high-performance insulation and energy-efficient heating elements helps reduce energy consumption while maintaining optimal performance.
5.Safety Features: Industrial ovens are equipped with safety features such as over-temperature protection, emergency shutoff mechanisms, and safety alarms, ensuring the safety of both operators and materials.
6.Durability: Made from high-quality materials such as stainless steel, these ovens are designed for long-lasting use and can withstand the rigors of continuous industrial operations.
Types of Industrial Ovens
1.Batch Ovens: These ovens are used for processing materials in batches, making them ideal for industries such as aerospace, automotive, and metalworking. They allow for easy loading and unloading of products, which is perfect for small to medium-scale operations.
2.Conveyor Ovens: Conveyor ovens are designed for continuous production lines. With a conveyor belt moving products through the oven, they are ideal for mass production processes in industries such as food manufacturing, electronics, and automotive parts production.
3.Walk-In Ovens: These large ovens allow workers to walk into the oven to load and unload products, making them ideal for larger components or when frequent access is needed. They are commonly used in industries like aerospace, automotive, and metalworking.
4.Tunnel Ovens: Typically used in continuous production processes, tunnel ovens are designed for large-scale applications, particularly in industries like food processing and packaging. Products move through a heated tunnel for uniform heating.
5.Laboratory Ovens: Designed for smaller-scale operations or research applications, laboratory ovens are used for processes like sterilization, drying, and testing under controlled temperature conditions.
Applications of Industrial Ovens
1.Automotive Industry: Used for curing automotive coatings, heat treating metal components, and curing rubber parts.
2.Aerospace: Industrial ovens are crucial for curing composite materials, heat treating metal parts, and conducting stress tests.
3.Food Processing: Industrial ovens are essential for baking, drying, sterilizing, and pasteurizing food products, such as snacks, meats, and beverages.
4.Electronics: Used for drying PCBs (printed circuit boards), curing solder, and testing electronic components.
5.Pharmaceuticals: Industrial ovens are used for sterilizing medical equipment, curing pharmaceutical coatings, and drying pharmaceutical products.
6.Metalworking and Manufacturing: Commonly used for heat treating metal components, including annealing, tempering, and hardening processes.
Advantages of Partnering with a Trusted Supplier
Customization Options: Whether you require specific dimensions, temperature settings, or special material compatibility, a reliable supplier will provide tailored solutions to meet your exact specifications.
Energy-Saving Design: Modern oven designs focus on lowering operational costs while maintaining high efficiency, integrating smart sensors and insulated enclosures to minimize energy waste.
Long-Term Durability: Industrial ovens are an investment—quality construction ensures long service life, even in intensive production environments.
Comprehensive Support: From pre-sales consultation and design engineering to installation, maintenance, and after-sales service, a trusted supplier provides full-cycle support.
Global Certifications: Leading suppliers manufacture ovens in compliance with international standards like CE, ISO, UL, and RoHS, ensuring safety and quality across global markets.
Frequently Asked Questions (FAQ) — Industrial Oven Factory
1. What types of industrial ovens do you manufacture?
We manufacture a wide range of industrial ovens, including batch ovens, conveyor ovens, walk-in ovens, tunnel ovens, and laboratory ovens. Each type is available with customization options to meet your specific processing requirements.
2. Can your industrial ovens be customized?
Yes, we offer fully customizable solutions including size, temperature range, heating method (electric or gas), air circulation system, and control interface (digital, PLC, touchscreen, etc.).
3. What is the typical temperature range of your ovens?
Our industrial ovens typically operate between 100°C and 1600°C, depending on the model and application. We can tailor ovens for lower or higher temperature needs upon request.
4. Which industries do you serve?
We supply industrial ovens to various industries such as automotive, aerospace, electronics, pharmaceuticals, food processing, and metalworking.
5. How accurate is the temperature control?
Our ovens offer high precision with temperature accuracy of ±1°C, ensuring uniform processing results and consistent product quality.
6. Do your ovens support international certifications?
Yes, our ovens can be manufactured in compliance with international standards such as CE, UL, ISO, and RoHS based on your regional and industry requirements.