The Nitrogen Debinding Oven utilizes advanced heating technology and a nitrogen protection system to provide a stable and oxygen-free high temperature environment for the material. In this environment, the organic matter in the material will be decomposed and volatilized rapidly, thus realizing the purpose of debinding. This equipment is widely used in powder metallurgy, ceramics, composite materials and other fields, is an indispensable part of the material preparation process.
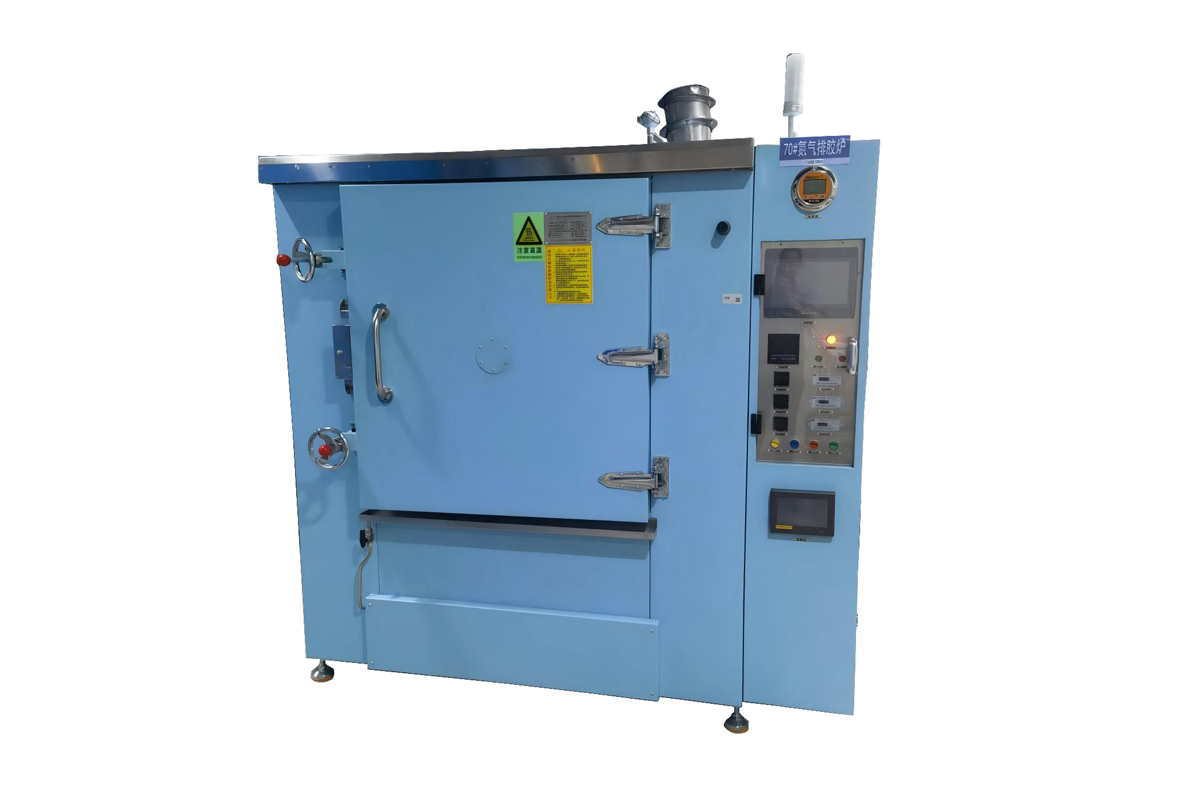
Working principle
1. Heating system: adopting high efficient heating elements (such as resistance wire, electric heat pipe, etc.), precisely controlling the temperature in the furnace through intelligent temperature control system, ensuring the material is discharged within the appropriate temperature range.
2. Nitrogen protection system: Continuously pass high purity nitrogen into the furnace to replace the air (mainly oxygen) in the furnace to form an oxygen-free inert gas environment. Nitrogen not only effectively prevents the material from oxidizing at high temperatures, but also promotes the volatilization and decomposition of organic substances.
3. Exhaust process: under the joint action of high temperature and nitrogen, the organic matter in the material begins to decompose and produce gas. These gases are discharged out of the furnace through the exhaust system of the furnace body, thus realizing the debinding of the material.
Product features
1. Efficient debinding: The combination of high temperature heating and nitrogen protection can quickly and thoroughly remove the organic matter in the material and improve the efficiency of debinding.
2. Prevent oxidization: Nitrogen as an inert gas can effectively protect the material from oxidization at high temperature and maintain the original performance and appearance of the material.
3. Precise temperature control: Adopting advanced temperature control system, it can accurately set and maintain the temperature in the furnace to ensure that the material is debinding within the optimal temperature range.
4. High safety performance: the equipment is usually equipped with over-temperature protection, overload protection and other safety devices to ensure that the power supply can be cut off in time under abnormal conditions and issue an alarm to prevent accidents.
5. Wide range of application: it is suitable for debinding of many materials, such as powder metallurgy products, ceramic products, composite materials, etc.
Application Areas
Nitrogen Debinding Oven has a wide range of applications in the following fields:
1. Powder metallurgy: It is used to remove the resin and other organic substances in powder metallurgy products to improve the density and strength of the products.
2. Ceramics manufacturing: In the process of preparing ceramic billets, it is used to remove organic substances in the billets to improve the sintering performance and final quality of ceramics.
3. Composite materials: In the preparation of composite materials, it is used to remove the resin and other organic substances in the materials to ensure the stability of composite materials.
Why Choose Our Nitrogen Debinding Oven?
High-precision design for critical industries
Reliable temperature accuracy and atmosphere control
Low maintenance and long service life
Global support, training, and remote diagnostics
Whether you are scaling up MIM/CIM production or optimizing your binder removal process for quality and yield, our Nitrogen Debinding Oven delivers the safety, consistency, and process control you need.
FAQ
What is a Nitrogen Debinding Oven?
A Nitrogen Debinding Oven is a specialized furnace used in the powder metallurgy and ceramics industries to remove binders from green parts (unfired objects) under a controlled nitrogen atmosphere. The process, known as debinding, is crucial for preparing materials before sintering.
Why is nitrogen used in the debinding process?
Nitrogen is used in the debinding process because it is an inert gas that prevents oxidation of the parts being treated. Its use ensures that the binder is removed without affecting the integrity of the material, especially when dealing with high-temperature processes.
What types of materials can be processed in a Nitrogen Debinding Oven?
The oven is typically used for processing metal powders, ceramics, and composite materials that have been bound together using organic binders. Common applications include the production of metal injection molded parts, ceramic components, and other advanced materials.
What is the main function of the Nitrogen Debinding Oven?
The primary function of the Nitrogen Debinding Oven is to remove organic binders from parts during the manufacturing process. This is a critical step before sintering, as it ensures that the final product has the required density and strength without contamination from binders.
How does the debinding process work in the oven?
During the debinding process, parts are placed in the oven, where they are heated in a controlled nitrogen atmosphere. The heat causes the organic binder to break down and evaporate. Nitrogen helps to ensure that this process occurs without causing oxidation or damage to the parts.
What temperature range does a Nitrogen Debinding Oven typically operate at?
Nitrogen Debinding Ovens generally operate at temperatures ranging from 300°C to 600°C (572°F to 1112°F), depending on the material being processed and the specific binder used.
What are the advantages of using a Nitrogen Debinding Oven?
The use of a Nitrogen Debinding Oven offers several advantages, including:
Inert atmosphere to prevent oxidation.
Precise temperature control for uniform debinding.
Reduced risk of part deformation during the debinding process.
Enhanced product quality by removing binders without damaging the material.
Is the Nitrogen Debinding Oven suitable for large-scale production?
Yes, Nitrogen Debinding Ovens are often designed for industrial use and can handle large quantities of parts at once. Many models are capable of processing multiple components in a single cycle, making them ideal for mass production environments.
What safety features should a Nitrogen Debinding Oven have?
A Nitrogen Debinding Oven should be equipped with several safety features, such as:
Pressure relief valves to prevent over-pressurization.
Temperature sensors and overheat protection to prevent accidental overheating.
Ventilation systems to ensure proper gas circulation and removal of vapors.
Automatic shutoff mechanisms in case of malfunction or failure.
How does a Nitrogen Debinding Oven improve manufacturing efficiency?
The Nitrogen Debinding Oven improves manufacturing efficiency by providing a controlled and consistent environment for the debinding process. It reduces the likelihood of defects, ensures the uniformity of parts, and helps streamline the production process, which ultimately enhances throughput and reduces production time.