It is widely used in factories and mining enterprises, petroleum, chemical industry, military, pyrotechnic explosives production, medical and pharmaceutical, universities and colleges scientific research, scientific research laboratories, paints and coatings and other related fields. The explosion-proof Oven adopts special design and manufacturing process, so that it can effectively prevent sparks, arcs and other fire or explosion hazards in the process of use.
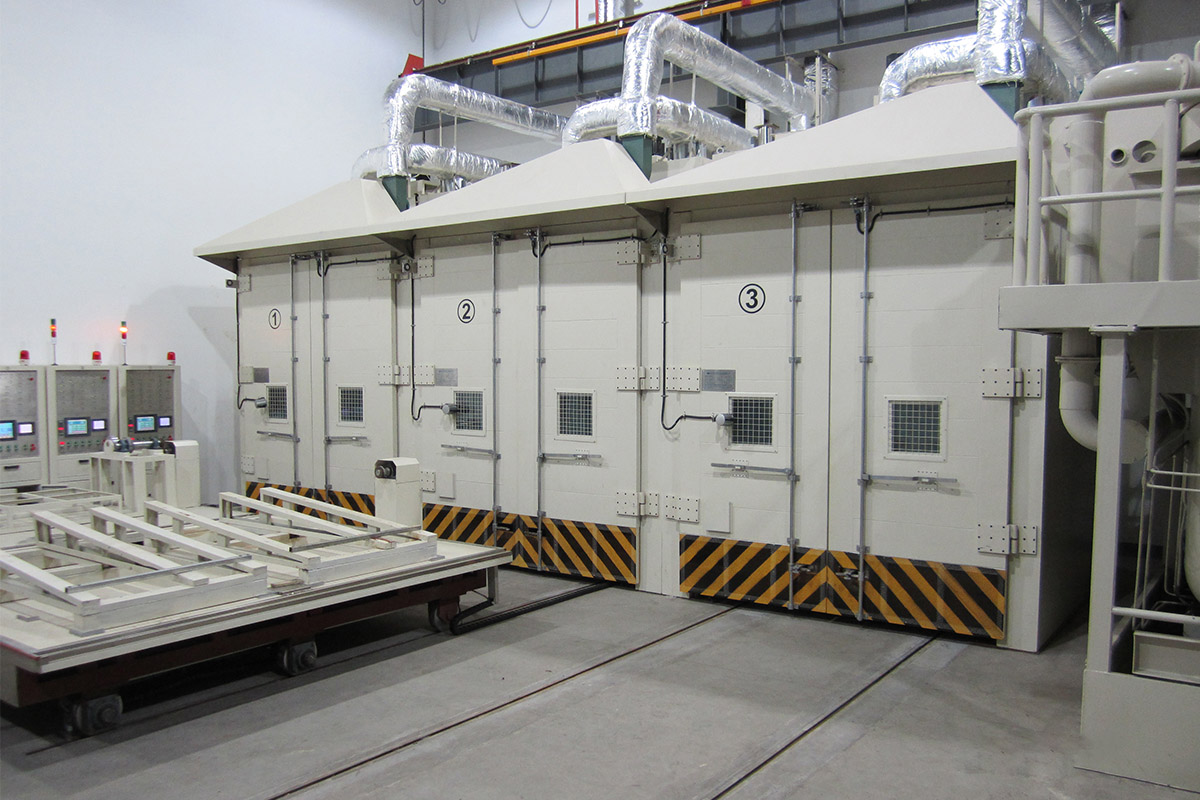
Equipment features
1. It adopts digital display intelligent temperature controller with microcomputer intelligent PID self-tuning function, which can be used for a long time without interruption. The system has temperature control, timing, over-temperature alarm function.
2. Adopting explosion-proof electrical components: the internal electrical components are all explosion-proof electrical components, such as explosion-proof motors, explosion-proof switches, etc., which have undergone strict explosion-proof treatment during the design and manufacturing process, and have high explosion-proof performance.
3. Adopting explosion-proof structure: electrical components are installed in explosion-proof electric box, which isolates the area that may generate sparks and arcs from other areas, thus effectively preventing sparks, arcs and other hazards that may cause fire or explosion.
4. The maximum temperature can reach 280 degrees, temperature control accuracy: ± 0.3 ℃%, temperature uniformity of 1.5 ℃%.
5. The inner liner is made of stainless steel plate precision welding, long-term use at high temperatures will not rust and deformation.
6. With exhaust device and air inlet adjustment device, so that the concentration of combustible gas in the box is always in the safe range.
Technical specifications for an Explosion-Proof Oven:
Technical Parameter | Specification |
---|
Explosion-Proof Level | Ex II 2G Ex d IIB T4 (can vary by requirement) |
Temperature Range | 50°C - 350°C (custom ranges available) |
Temperature Uniformity | ±2°C |
Temperature Control Accuracy | ±1°C |
Heating Power | 3kW - 30kW (based on Oven size and requirements) |
Capacity | 30L - 1000L (custom sizes available) |
Interior Material | Stainless Steel 304/316 |
Exterior Material | Galvanized Steel, Aluminum Alloy, or Custom |
Heating Method | Electric Heating, Forced Hot Air, Infrared Heating |
Control System | PLC Control System, Touch Screen Optional |
Power Supply | 220V/380V 50Hz (Other voltages available) |
Air Circulation | High-temperature, Corrosion-Resistant Fans |
Safety Features | Over-temperature Protection, Pressure Relief Valve, Emergency Stop |
Explosion-Proof Components | Enclosed Electric Parts, Sealed Switches, Explosion-Proof Glass Windows |
Cooling System | Optional Rapid Air Cooling or Natural Cooling |
Data Logging | Yes, with Real-Time Monitoring Capabilities |
Alarm System | Visual and Audible Over-Temperature Alarm |
Door Seal Type | High-Temperature Resistant Silicone Seals |
Weight | Varies by model (from 50kg to over 500kg) |
Dimensions (HxWxD) | Customized to user needs |
Installation Type | Stand-alone or Built-in Options |
Certification | ATEX, IECEx, CE, RoHS, GB (varies by region) |
Warranty | Typically 1-2 years, extendable |
Design and Structural Features
Explosion-Proof Enclosure:
The exterior casing is constructed from robust, explosion-proof materials, often stainless steel, galvanized steel, or aluminum alloy, to withstand harsh conditions.
It features high sealing capability, effectively preventing any sparks or arcs from escaping.
All electrical components are isolated and protected, meeting international and domestic explosion-proof standards such as ATEX, IECEx, and GB.
Precise Temperature Control System:
Equipped with high-precision temperature controllers, allowing accurate temperature adjustments ranging from ambient temperature to above 300°C (depending on the model).
The temperature control system includes over-temperature alarms and automatic shut-off to prevent hazardous temperature overshoots.
Smart temperature controllers can connect to data logging devices for real-time monitoring and storage of temperature data.
Uniform Heating System:
The internal heating system is designed with multiple distribution points to ensure even temperature distribution throughout the interior.
Uses electric heating or forced hot air circulation to efficiently heat workpieces while maintaining consistent thermal distribution.
The hot air circulation system utilizes high-temperature and corrosion-resistant fans to guarantee stable airflow, minimizing localized overheating.
Safety Protection Features:
Comes with explosion pressure relief valves that quickly release pressure in case of abnormal buildup, preventing potential explosions.
Equipped with relief devices and explosion-proof windows, allowing operators to safely observe the Oven’s interior.
Features multiple layers of safety protection, including overload protection, short-circuit protection, leakage protection, and emergency stop buttons to ensure operational safety.
Key Advantages
Safety and Reliability: Explosion-proof ovens are rigorously certified to ensure that all components meet safety standards, allowing them to operate safely in hazardous areas.
High Efficiency and Energy Saving: High heating efficiency with optimized energy usage, reducing energy consumption through intelligent controls.
Versatile Applications: Suitable for a variety of heating, drying, and curing processes, catering to different industrial needs.
Customizable Options: Customizable heating modes, explosion-proof levels, capacity, temperature ranges, and materials based on customer requirements.
Application Fields
Chemical Industry:
Drying and removing volatile solvents, such as chemicals and intermediates.
Ideal for heating sensitive chemicals in a controlled environment.
Pharmaceutical Industry:
Oil and Gas:
Coating and Painting Industry:
Rapid drying and curing of paints and coatings, especially in hazardous environments.
Low-temperature drying of sensitive coating materials to prevent unwanted chemical reactions.
Military and Defense Industry:
Safety Operating Guidelines
Pre-Operation Checks:
Ensure the equipment is installed in an explosion-proof compliant area, and all electrical connections meet safety standards.
Inspect the seals and explosion-proof components for integrity, ensuring no signs of damage or wear.
During Operation:
Regular Maintenance:
Regularly check the condition of internal electrical components and replace aging parts promptly.
Clean the interior after each use to prevent the buildup of flammable substances.
Conduct periodic explosion-proof tests to ensure compliance with the latest safety standards.
FAQ
1.What is an Explosion-Proof Oven?
An Explosion-Proof Oven is a specialized industrial heating device designed to operate safely in environments where there are flammable or explosive gases, vapors, or dust. It is engineered to prevent internal or external sparks from igniting hazardous materials, ensuring safe operation in high-risk settings.
2. What industries commonly use Explosion-Proof Ovens?
Explosion-Proof Ovens are widely used in the chemical, pharmaceutical, oil and gas, coatings, military, and electronics industries. These industries often deal with flammable substances, making safety-critical equipment necessary for processing, drying, or curing materials.
3. How does an Explosion-Proof Oven prevent explosions?
Explosion-Proof Ovens have multiple safety features, such as robust explosion-proof enclosures, sealed electrical components, pressure relief valves, and high-temperature-resistant seals. These measures prevent the escape of sparks and arcs that could ignite hazardous substances, ensuring a controlled and safe environment.
4. What temperature range can Explosion-Proof Ovens handle?
Most Explosion-Proof Ovens have a temperature range of 50°C to 350°C, though some models can handle higher temperatures. The specific range can be customized based on the application and industry requirements.
5. What are the key safety features of an Explosion-Proof Oven?
Key safety features include over-temperature protection, explosion pressure relief valves, emergency stop buttons, explosion-proof windows for observation, and sealed components to prevent sparks. Additionally, some models come with data logging and alarm systems for enhanced safety monitoring.
6. How is temperature controlled in an Explosion-Proof Oven?
Temperature is controlled using high-precision temperature controllers, often with PLC (Programmable Logic Controller) systems. These controllers allow accurate temperature adjustments, monitoring, and real-time data logging. They include safety features to shut down operations in case of temperature anomalies.
7. Can Explosion-Proof Ovens be customized?
Yes, Explosion-Proof Ovens are often customizable to meet specific industry needs. Custom options may include different explosion-proof levels, capacity, temperature ranges, heating methods, material choices, and control systems. This ensures the oven is suitable for various hazardous environments.
8. What is the difference between a standard oven and an Explosion-Proof Oven?
A standard oven is designed for general-purpose heating and drying without additional safety features for hazardous environments. An Explosion-Proof Oven, on the other hand, is specifically designed with safety in mind, equipped with components that prevent ignition sources, comply with strict safety standards, and provide protective measures against explosive risks.
9. What certifications should an Explosion-Proof Oven have?
An Explosion-Proof Oven should have certifications like ATEX (for Europe), IECEx (International), UL (United States), GB (China), and CE. These certifications ensure the oven meets international safety standards for operation in hazardous environments.
10. What maintenance is required for an Explosion-Proof Oven?
Regular maintenance includes inspecting seals, checking explosion-proof components, cleaning the interior to prevent buildup of flammable materials, replacing worn parts, and conducting periodic safety tests to ensure continued compliance with explosion-proof standards. Proper maintenance prolongs the oven's lifespan and maintains safety standards.